What is the FAE ESD Room?
In this video we present the 180m2 ESD Room – Electrostatic Discharge Room, with electrostatically discharged dissipative flooring to minimize the possibility of damaging FAE electronic components sensitive to electrostatic discharge.
A room dedicated exclusively to manufacturing Absolute Pressure Sensors (MAP), Exhaust Gas Pressure Sensors (EGPS) and Gear Position Sensors (GPS). It has a dosing station in which various Coating, Potting, Sealing processes are carried out automatically. It has a large manufacturing capacity of 500,000 units/year per shift and all the products are manufactured in the Barcelona plants, under the IATF 16949 standard.
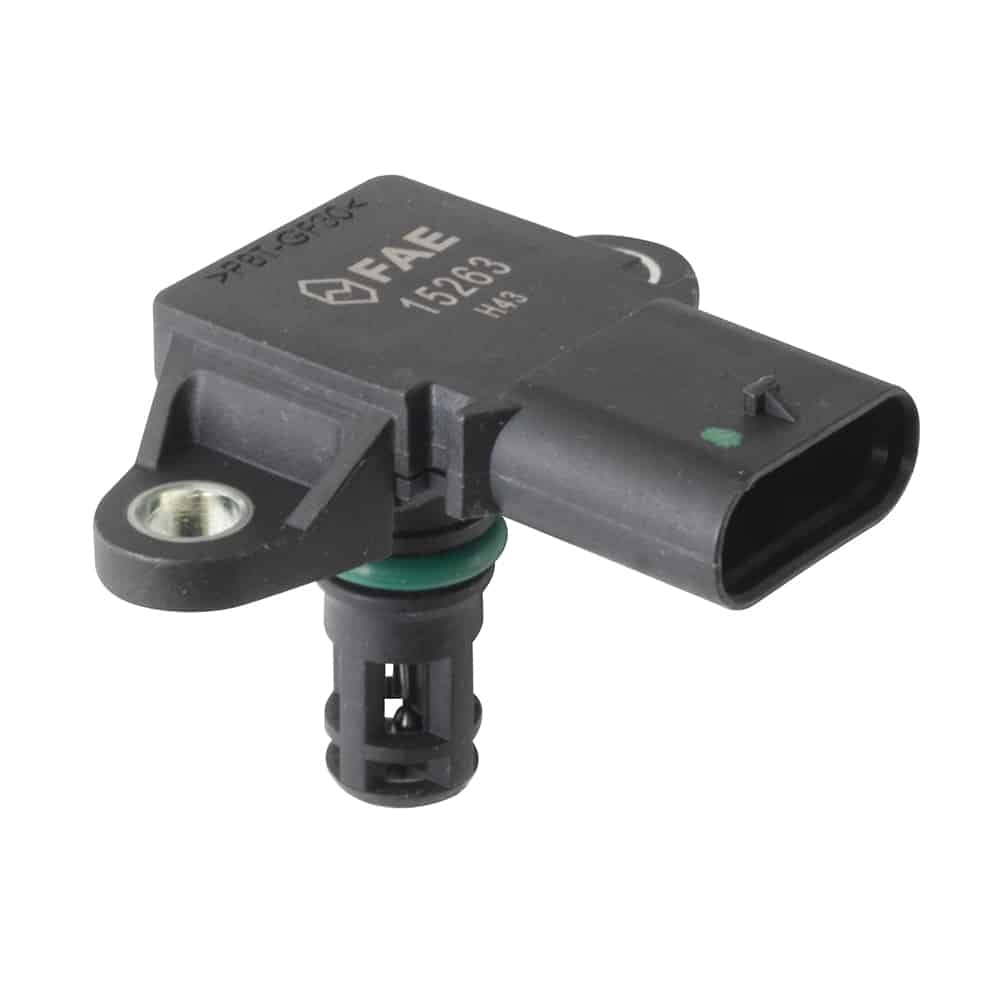
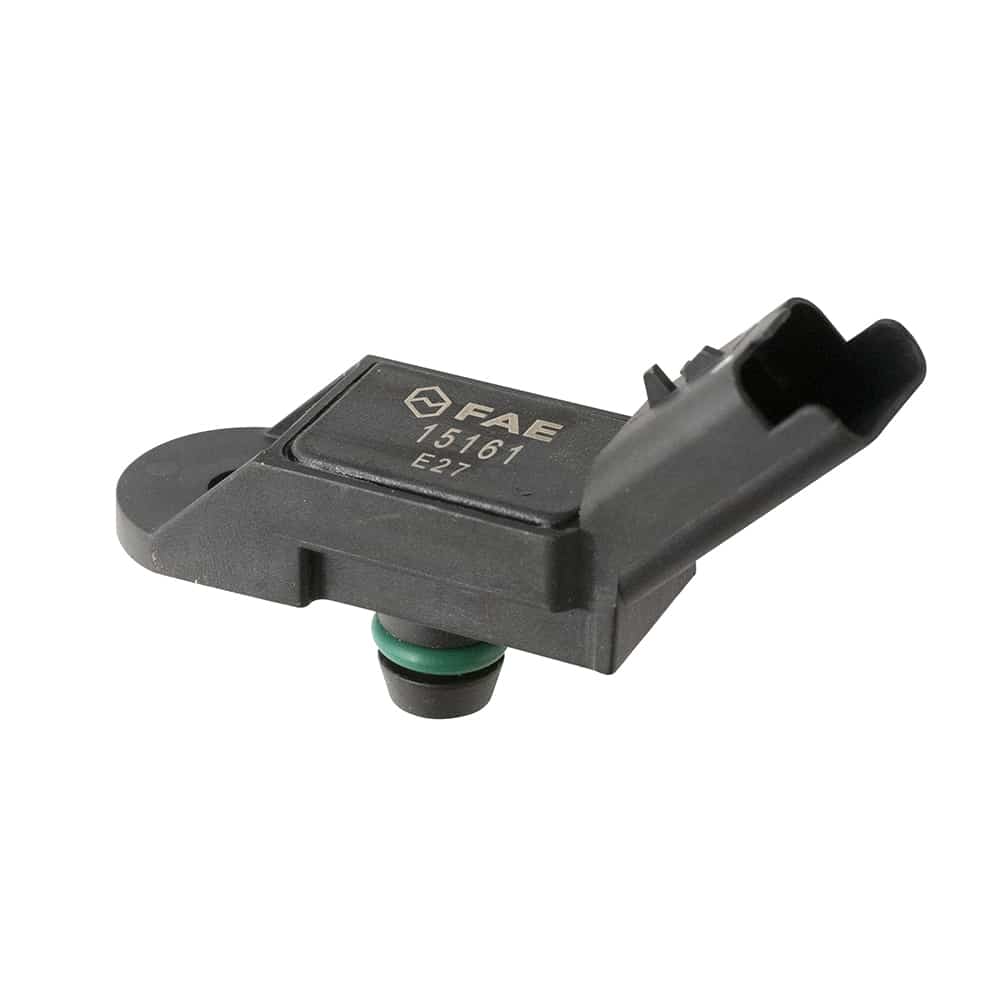
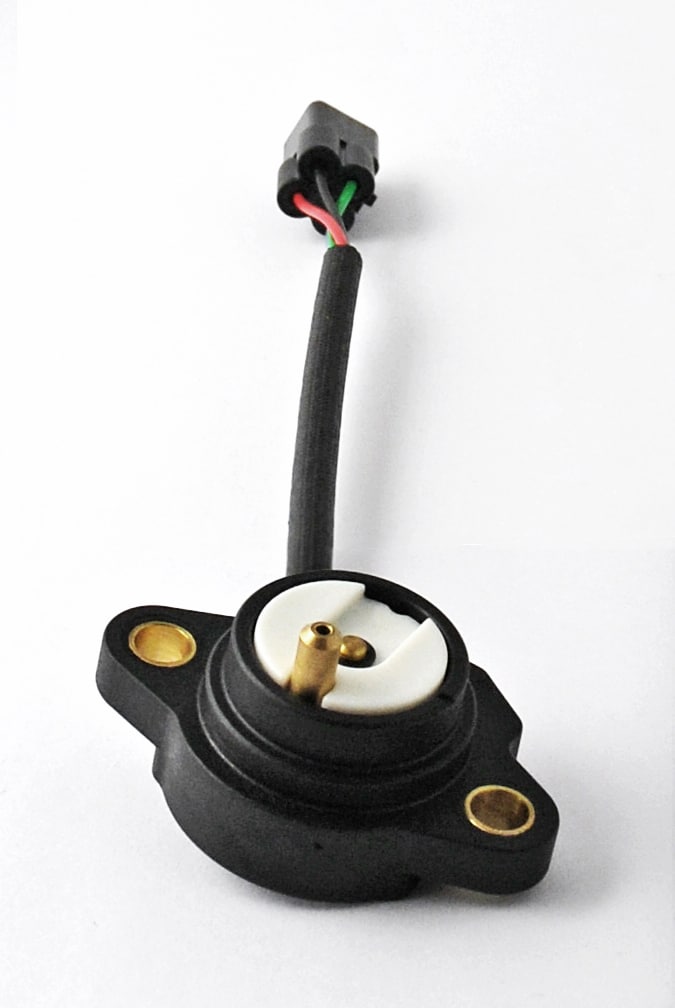
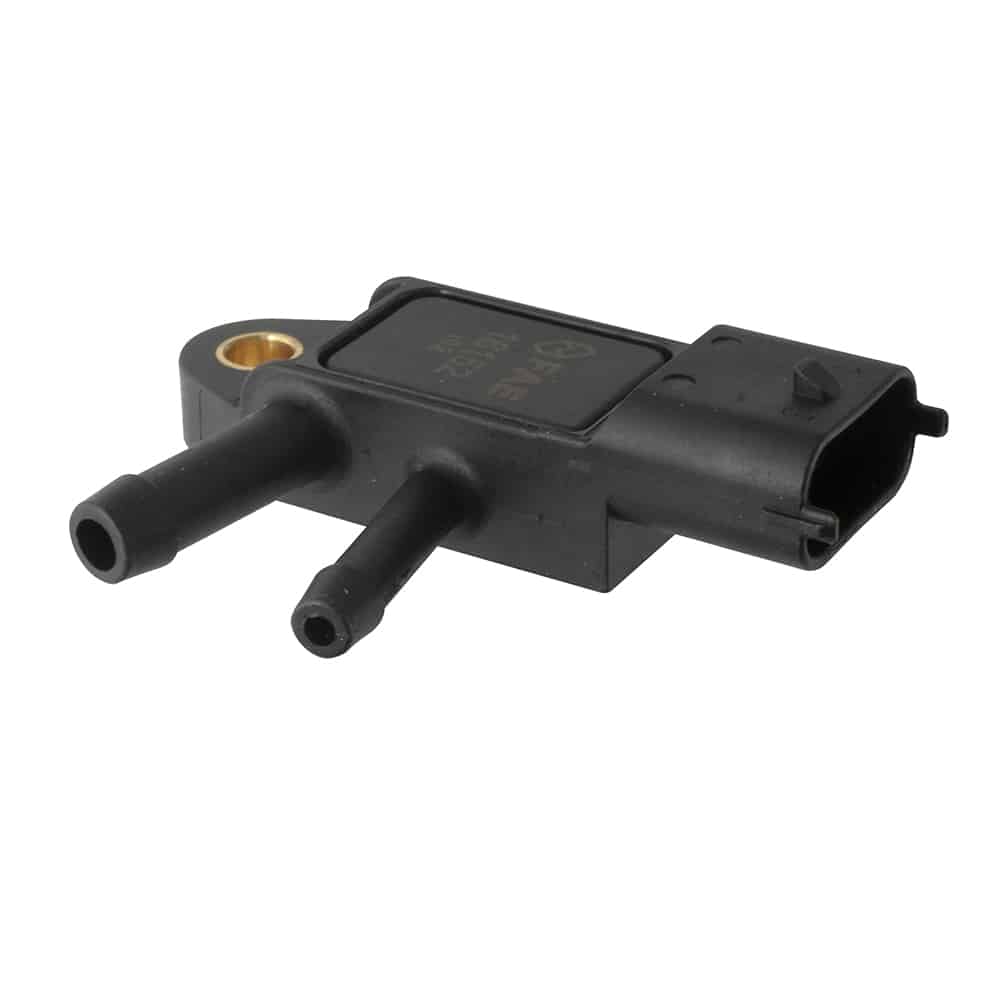
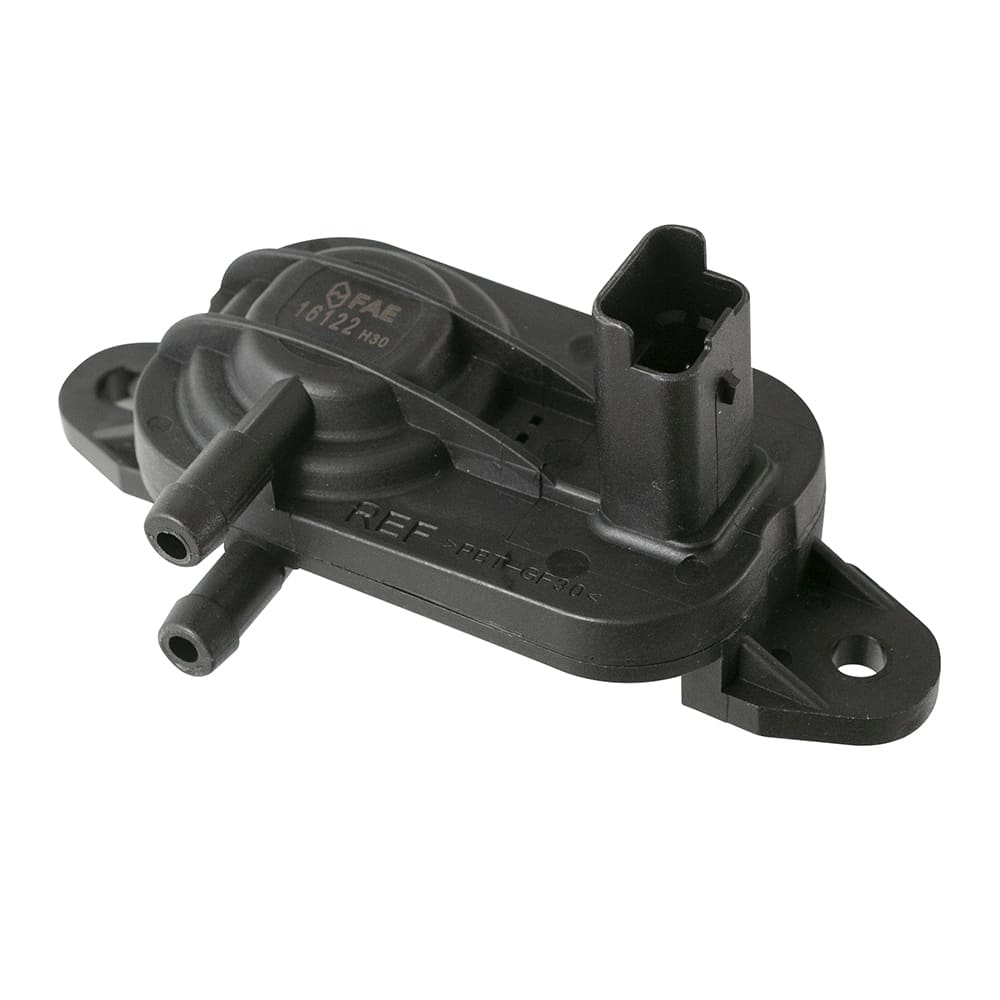
What are the production phases inside the room?
The most relevant production phases for the manufacture in an ESD Room of the different types of sensor are the Coating, Potting and Sealing processes.
We summarize them briefly.
Coating: The Coating process involves the application of a protective coating to the surface of electronic components or printed circuit boards (PCBs) to provide protection against moisture, corrosion, or other environmental factors. In an ESD room, it is done following rigorous static control standards to prevent damage to sensitive components. Se utilizan materiales de recubrimiento especiales que son disipativos o conductivos para evitar la acumulación de cargas electrostáticas. Además, se deben utilizar equipos y herramientas adecuadas para garantizar una aplicación uniforme y precisa del recubrimiento.
Potting (Assembly): The Potting process involves the assembly or assembly of electronic components on PCBs or other substrates. This process is done inside an ESD room to prevent damage from electrostatic discharge. Operators must follow strict static control guidelines, such as the use of antistatic wrist straps and conductive workbenches. In addition, methods of handling and transporting components that minimize the risk of generation or accumulation of electrostatic charges can be used. This includes the use of antistatic trays or containers and careful handling of components to avoid damage from electrostatic discharge.
Sealing: The Sealing process involves the application of sealants or adhesives to electronic assemblies to provide mechanical protection and protect against moisture, dust, or contamination. In an industrial environment within an ESD room, static control protocols must be followed to avoid problems caused by electrostatic discharge. Sealants and adhesives used must be suitable for use on electronic components and must be applied using methods that minimize the risk of generating electrostatic charges. In addition, operators must use proper equipment and tools and ensure that work areas are designed to safely control and dissipate static electricity.
What is electrostatic discharge?
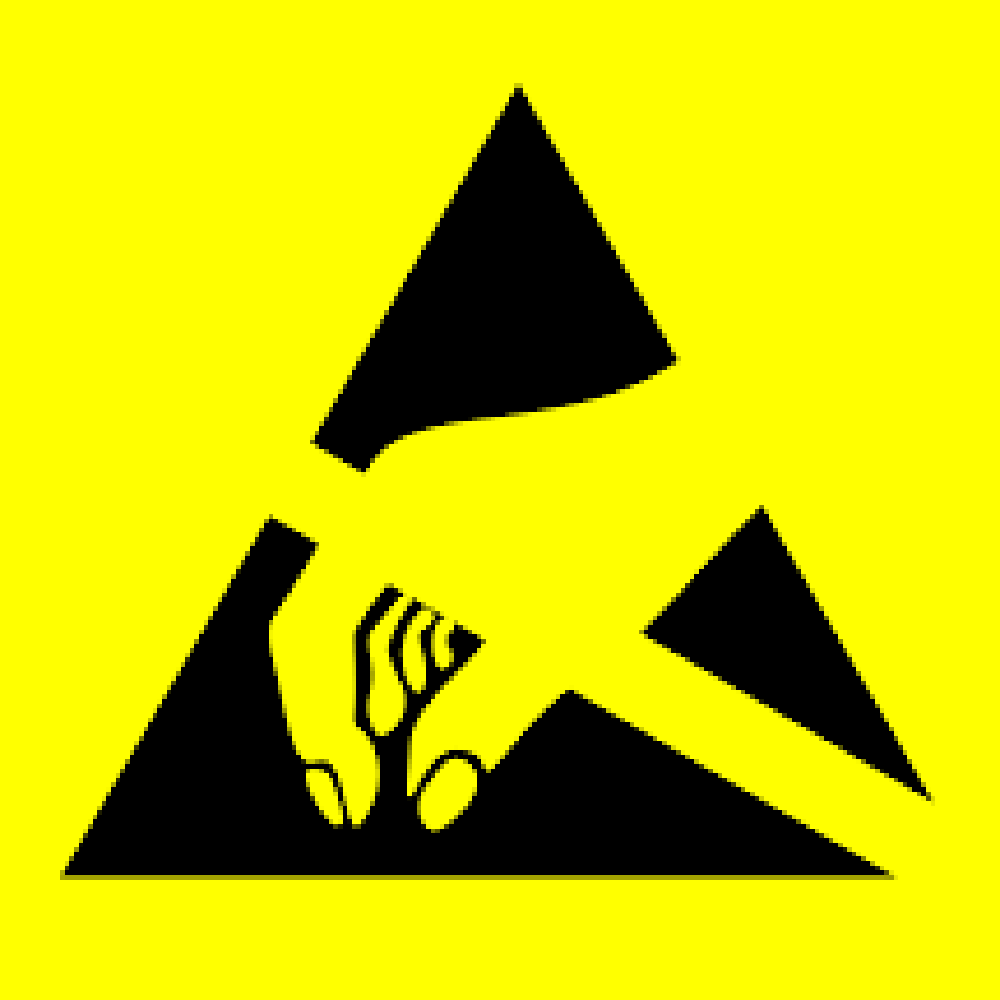
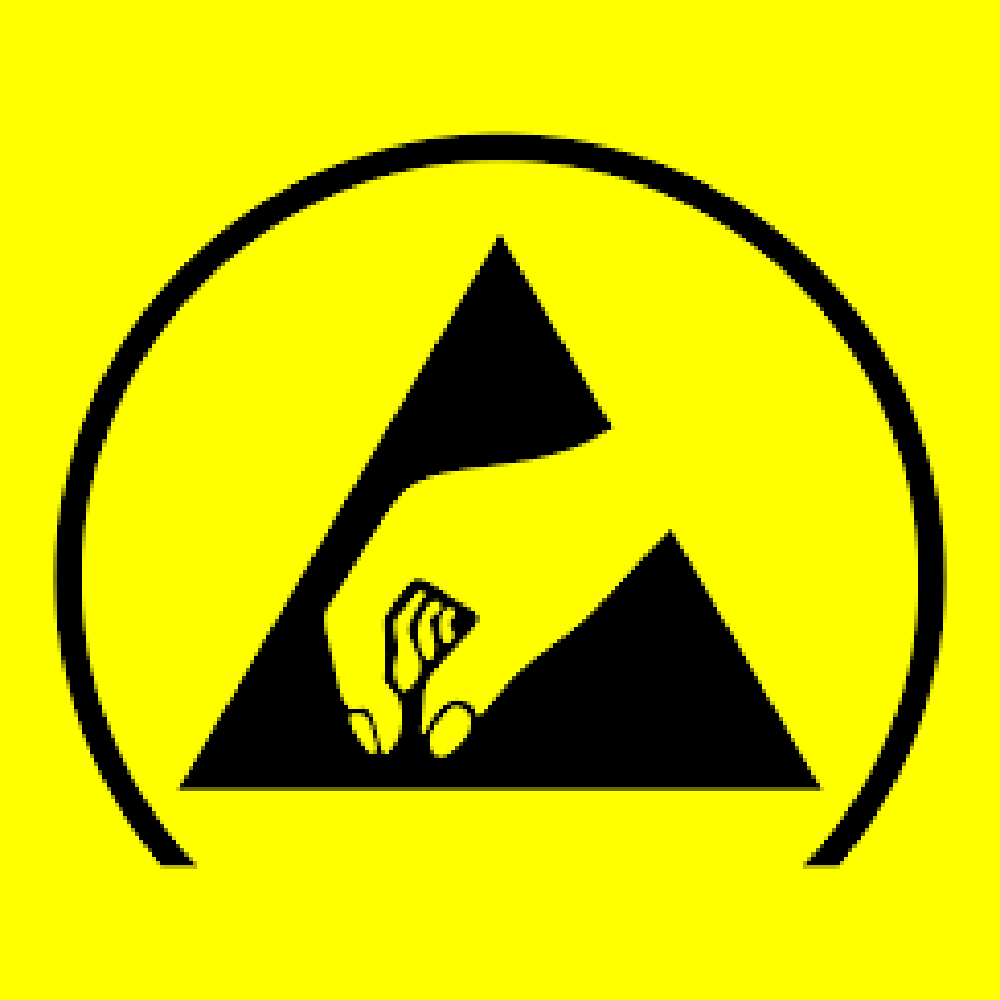
Electrostatic discharge refers to the sudden flow of electricity between two objects with different electrical charges. It occurs when there is a buildup of static electricity on an object and then a rapid transfer of charge occurs through an electrical arc.
Static electricity can build up on objects due to friction, contact with charged surfaces, or electrostatic induction. When two objects with different electrical charges come close enough or come into contact, an electrostatic discharge occurs.
Electrostatic discharge can have negative consequences, especially in sensitive environments such as electronics and electronic components. It can damage or destroy sensitive components, cause errors in electronic devices, and lead to system failure.
How can we prevent electrostatic discharge?
To prevent electrostatic discharge and minimize its negative effects on sensitive electronic components, a number of protective measures are implemented. These measures are designed to safely control and dissipate static electricity accumulated on objects and prevent its uncontrolled transfer.
Some of the more common measurements include:
Grounding Devices: Grounds are used to provide a safe discharge path for static electricity. This involves grounding objects and equipment using grounding cords or plugs. By doing so, any accumulated electrical charge will dissipate in a controlled manner towards the earth, thus avoiding the possibility of harmful electrostatic discharge.
Anti-static wrist straps: These wrist straps are commonly used in environments where sensitive electronic components are handled. They are placed around the operator’s wrist and are connected to a ground connection. The bracelets help divert any electrical charge accumulated in the human body towards the earth, preventing it from being transferred to electronic components.
Conductive mats and workbenches: These special surfaces are designed to safely dissipate static electricity. They are made of conductive materials or have a conductive layer that allows any electrical charge to gradually discharge toward the earth. Conductive mats and workbenches are used in areas where electronic components are handled to prevent static electricity buildup.
Anti-static packaging and containers: The materials used in the packaging and containers of sensitive electronic components are designed to dissipate static electricity effectively. These materials, such as antistatic bags and boxes, prevent electrical charges from building up inside and protect components from possible ESD damage.
Humidity Control: Proper relative humidity can help prevent static electricity buildup. By maintaining controlled humidity levels in the work environment, the generation and accumulation of static electrical charges can be reduced.
These protection measures are implemented in a combined manner and adapted to the specific needs of each work environment. By following proper ESD prevention practices, the integrity and reliability of sensitive electronic components can be ensured, thus preventing costly damage and failure of electronic systems.