In this report we will talk about the Lambda Sensors we manufacture at FAE and the evolution of this product over the years.
1. INTRODUCTION TO THE OXYGEN SENSOR
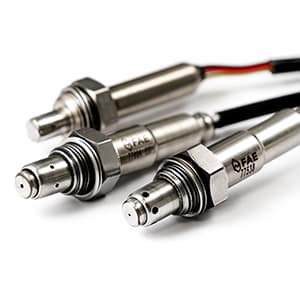
Crude oil is running out and we’re moving, in leaps and bounds, towards the electric vehicle. But this transition to a 100% clean vehicle must be done by improving the efficiency and ecology of the current combustion vehicles, which still have many years of life in the market.
And, although it seems ironic to speak of ecology when we’re referring to vehicles that pollute the environment, we can assure you that the technological advances of recent years are contributing to the drastic reduction of harmful gas emissions into the atmosphere, which are responsible for the greenhouse effect.
According to a recent study of the AMB (Metropolitan Area of Barcelona) with regard to PM (Particle Matter), 1 20-year-old car pollutes as much as 36 modern-day cars and, in the case of NOx (Nitrogen Oxide), pollutes as much as 5 modern-day cars. Looking at the motorcycle statistics, the ratio is 1:17.
For this reason, the European authorities who regulate exhaust emissions have set out increasingly restrictive policies. From the 90s until now, EU standards have got increasingly stronger with the enactment of consecutive directives from Euro2, Euro3, up to the current Euro6c. Some manufacturers have had problems and have not passed the tests, which has posed a great challenge to engineers of engines, afterburner systems and the design of lambda probes.
Gas emission control is handled by software managed by the ECU (Engine Control Unit), the brain of the vehicle. In the same way that our brain makes the decision to move our hand if we notice that it is burning, any decision made by the ECU depends directly on what is indicated by the sensors distributed throughout the vehicle. One of these sensors is located in the exhaust pipe and is precisely responsible for reducing the emission of harmful gases into the atmosphere, it is the well-known lambda sensor (also called oxygen sensorIt continuously detects the proportion of oxygen in the remaining exhaust gas, so that the ECU can adjust the amount of fuel required to the optimum value.
All vehicles with a catalytic converter have at least one Lambda Probe (regulating) which is located before the catalytic converter. However, vehicles that apply the OBD (On-Board Diagnostic) systems, are equipped with a second Lambda Probe (diagnostic) which is located on the back of the catalytic converter and reports on the correct operation of the regulating Lambda Probe while also correcting any deviation. These probes also control the life cycle of the catalytic converter, letting us know when it’s exhausted and needs to be replaced.
But why is it called a Lambda Probe? Well, the Lambda factor (ƛ) indicates the air-fuel ratio compared to the ideal stoichiometric ratio of 14.7 parts air to 1 part fuel (in weight). If this comparison gives a lambda factor greater than 1, then we have a fuel-lean mixture. If the lambda factor is less than 1, we have a fuel-rich mixture.
2. COMPONENTS OF THE OXYGEN SENSOR
CABLE
Cable sheathing made of fluoropolymer with high performance at extreme temperatures.
CERAMIC CLAMP
Complete assembly at our facilities.
CERAMIC INSULATORS
Technical ceramics designed to ensure watertightness and avoid contamination. IP68 water resistance protection degree, able to operate in continuous water immersion.
SENSOR
Multilayer ceramic planar sensor technology. Manufactured in controlled clean room type environments.
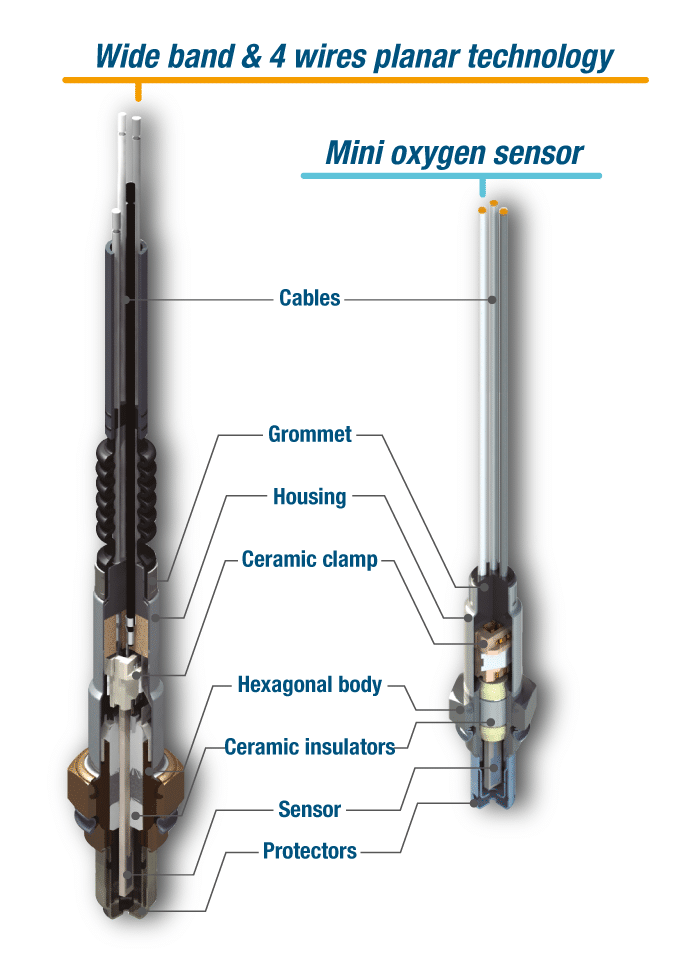
3. TECHNOLOGICAL EVOLUTION OF OXYGEN SENSORS
It is important to know that the first lambda sensors date back to the 70’s, where the EGO (Exhaust Gas Oxygen Sensor) type sensors of that time were not heatable and had a useful response time of more than 120 seconds. This meant that, from the time the vehicle was started, the ECU did not receive a clear reading until after 2 minutes, when the cold engine pollutes the most.
Generally speaking, it can be said that, during all these years, the speed, stability and accuracy of the lambda sensor’s response have been improved, regardless of the engine speed, and a shorter commissioning time, i.e. the time it takes for the sensor to reach the working temperature, as well as its resistance and durability.
The evolution has been considerable, highlighting the introduction of heatable oxygen sensors, the appearance of oxygen sensors with proportional response to the lambda parameter, also known as wideband oxygen sensor or AFR. (Air Fuel Ratio)and the development of the planar technology, in which the Spanish company FAE – Francisco Albero, S.A.U., has made a very strong commitment, since it has been developing its own planar technology for years, putting into operation a Clean Room of more than 700 m2 of space.2 for the development and manufacture of thousands of high-tech, high-quality lambda sensors and probes for customers around the world.
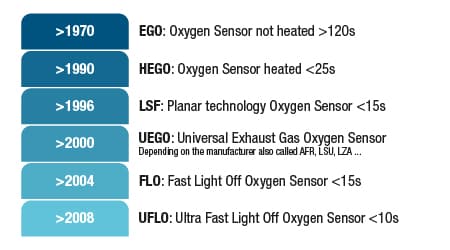
4. TYPES OF OXYGEN SENSORS
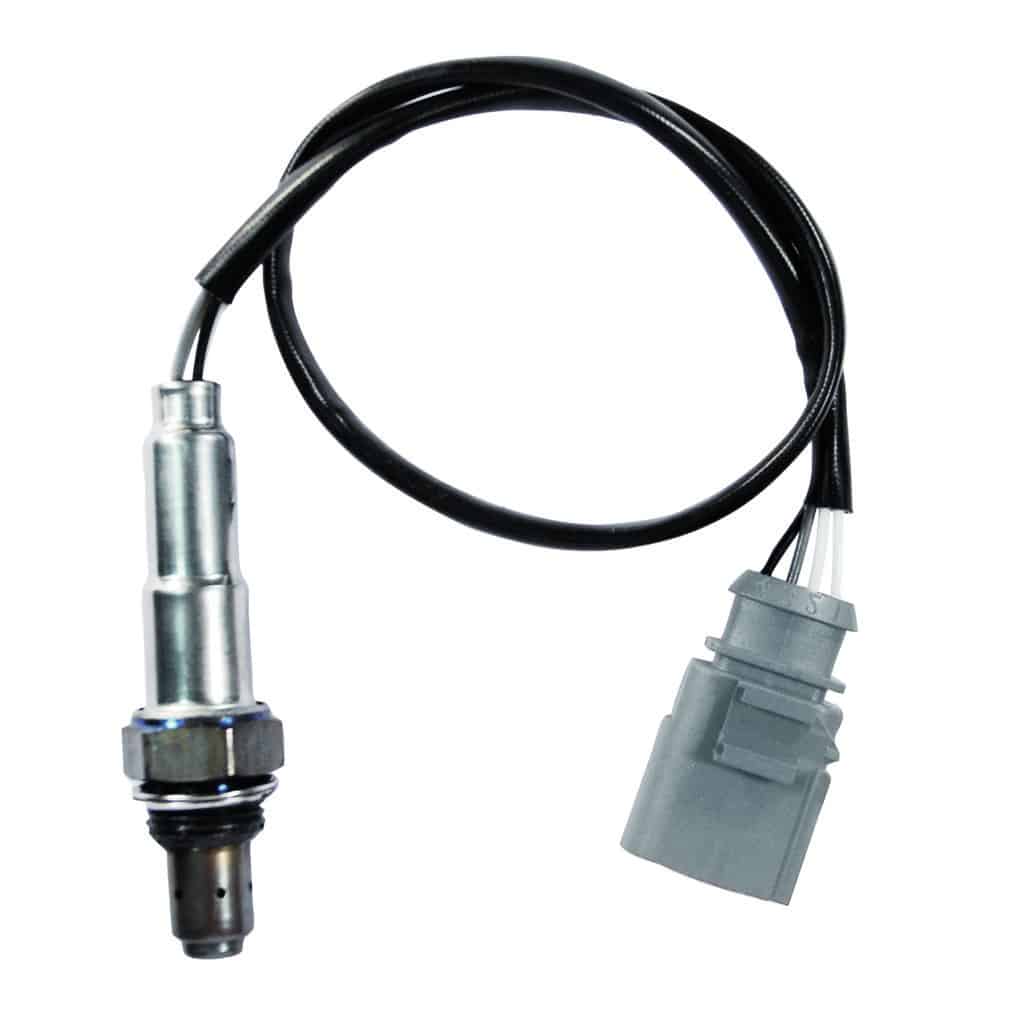
4.1 Zirconium oxygen sensors
Binary oxygen sensors, made of zirconium dioxide or zirconia ceramic, contain a solid electrolyte that provides an electrical voltage obtained by comparison of two atmospheres (exhaust gases on one side and outside air on the other) and is sensitive to the concentration of oxygen in the exhaust gases. Fuel-rich mixtures produce a high voltage and lean mixtures produce a low voltage, thus giving an on-off binary response with only two values: 0 or 1, easily interpretable by the electronics.
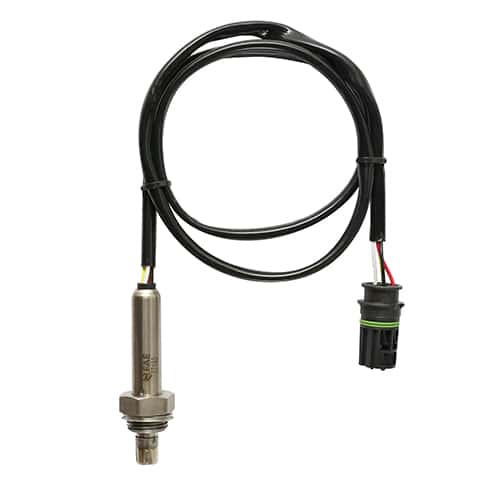
4.2 Titanium oxygen sensors
This probe’s sensor is made of a Titanium Dioxide ceramic element. Unlike the Lambda Probes based on Zirconium Dioxide, these do not generate any voltage, and the sensor material is submerged in the exhaust gases without the need for outside air.
These oxygen sensors always include a heater, and, at high temperatures, the resistance of this material is sensitive to the difference in oxygen concentration of the exhaust gases. For a fuel-rich mixture, the resistance drops to minimum values and for a fuel-lean mixture, it rises to maximum values. The ECU powers the oxygen sensors with a fixed voltage and reads the response of the oxygen sensor through a voltage divider circuit.
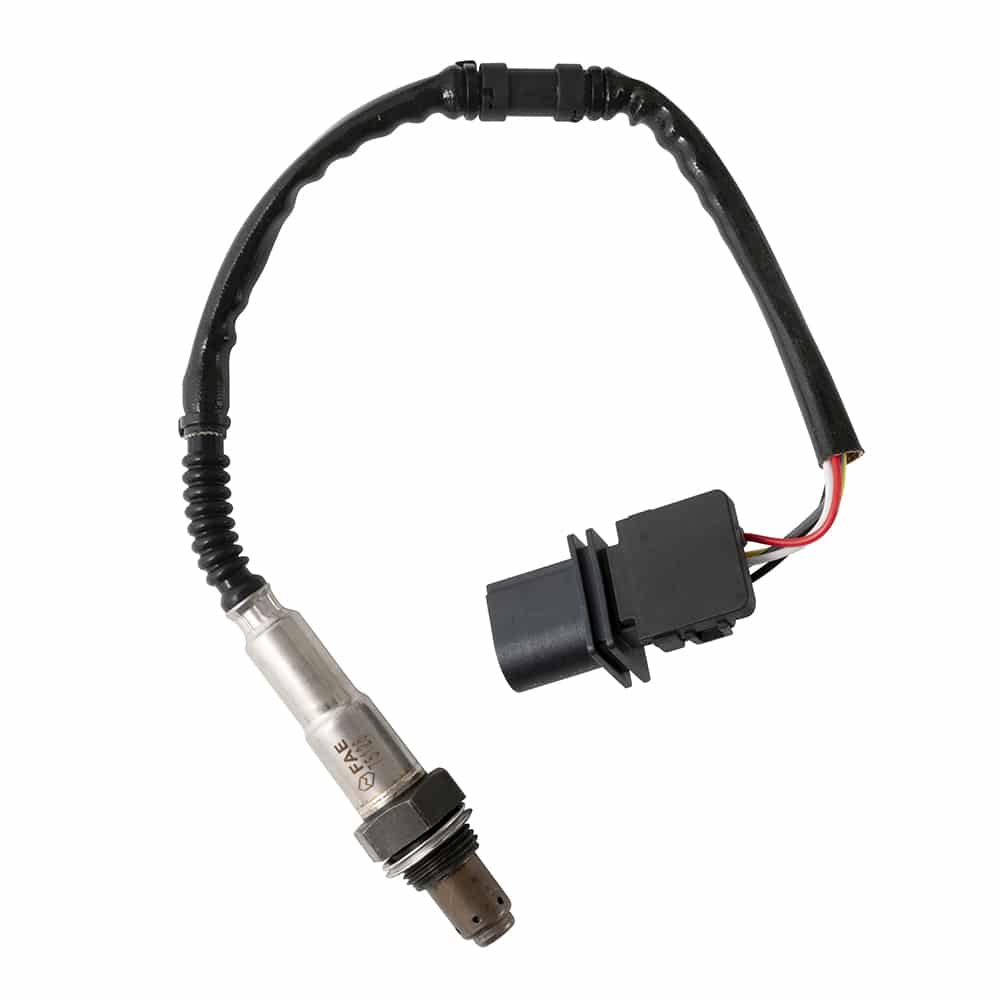
4.3 Wideband oxygen sensors
Unlike the binary Zirconia oxygen sensors, the Wideband oxygen sensors provide a continuous, non-binary response to the detected lambda value. Therefore, they measure the composition of the exhaust gases with great accuracy, which also makes them suitable for diesel and gasoline engines.
These contain two electrochemical cells that work concurrently. One of them measures the rich or lean character of the gas mixture, similar to the binary oxygen sensors. The reaction of the other electrochemical cell is influenced by the signal of the first cell and by the amount of oxygen in the combustion gas. The joint functioning of the two cells provides a positive electric current for lean mixtures, negative for rich mixtures and zero in the case of a perfect or stoichiometric mix.
The current generated by the Wideband oxygen sensors is calibrated and must also be transformed into voltage so that it can be read by the vehicle’s ECU. For this reason, the oxygen sensor has in-built calibration resistance in the connector. This resistance is different for each probe, so you should not, under any circumstances, replace one oxygen sensor with another by cutting the wires.
First generation wideband oxygen sensor:
They contain an external air reference channel similar to that of the binary Zirconia oxygen sensors.
Second generation wideband oxygen sensor:
They do not need this reference channel to operate. Compared to first generation oxygen sensors, the absence of a channel saves the power consumed by these oxygen sensors, the initial warm-up time is shorter and the stability of the signal throughout their lifetime is greater.
Depending on the application of each vehicle, a first or second generation wideband oxygen sensor is required, but they are not interchangeable.
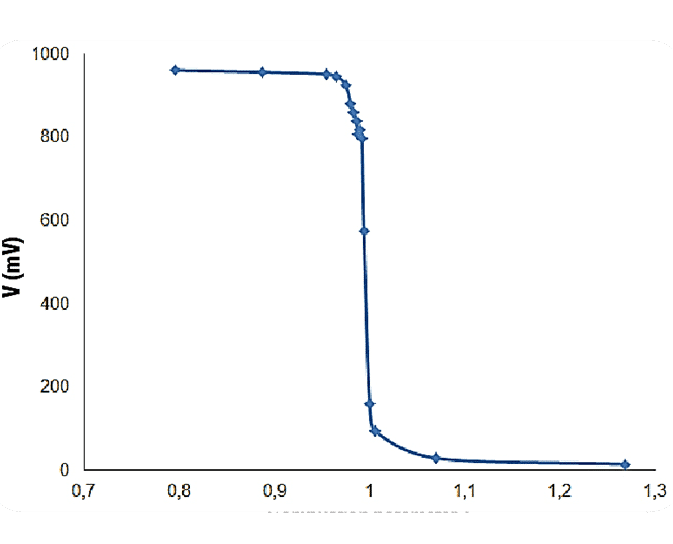
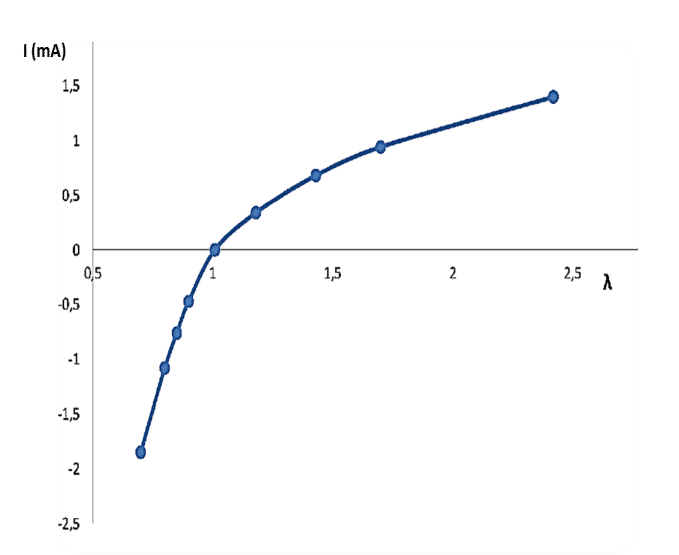
Difference Difference in the response between a binary Zirconia oxygen sensor and an Air Fuel Ratio oxygen sensor; the first is a binary response (1 or 0) but in the Air Fuel Ratio the response is progressive, so the ECU can accurately measure the composition of the exhaust gases at all times and therefore act with greater precision; the response of the binary Zirconia only reports whether the mixture is rich or lean, but not the exact level of the gas mixture.
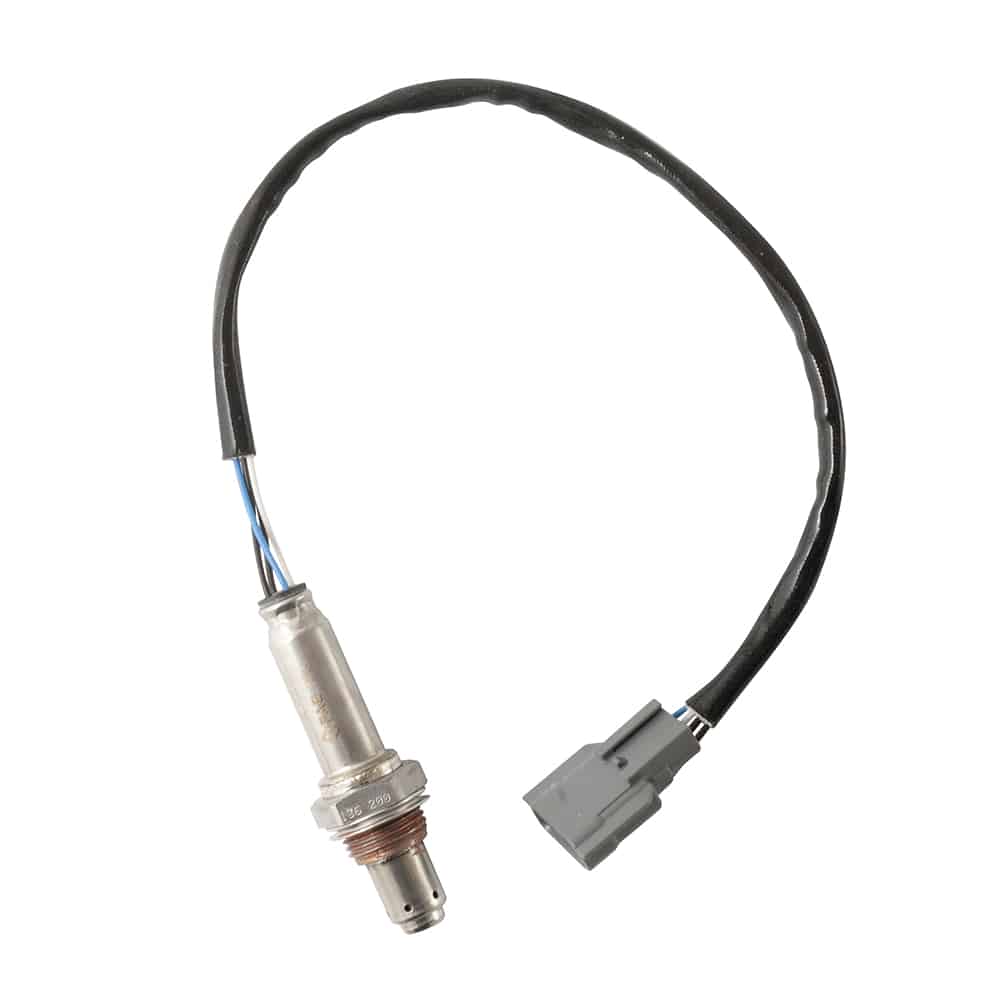
4.4 Air Fuel Ratio A/F oxygen sensors
These are 4-wire Wide Band sensors, which provide a proportional signal (figure 11) against the detected lambda value, but with a single electrochemical cell. This cell is regulated by the vehicle electronics and reacts conditioned by the amount of oxygen present in the combustion gas simultaneously. The combined operation provides a characteristic current corresponding to the different gas compositions in the exhaust pipe without the need for prior individual calibration. The current generated is positive for lean mixtures where it is able to measure the gas composition with high accuracy and, in turn, due to its non-limiting reference channel, is sensitive to rich, oxygen-free mixtures by being able to generate current in the opposite direction; this makes it suitable not only for diesel engines, but for petrol engines too.
This sensor is equivalent to a 5-wire wideband oxygen sensor in terms of response, because the signal it gives is proportional to the oxygen sensor, it also gives a more efficient control of emissions, however, unlike the 5-wire ones, this sensor requires only one electronic cell, which implies less use of platinum.